[ Instrument Network Instrument Development ] Boiling heat transfer is an extremely efficient phase change heat transfer technology. It has the advantages of high heat flux density, low superheat and good temperature uniformity. Therefore, it is used in heat transfer, conversion and management systems. It plays a vital role and is widely used in power generation, desalination, metallurgy, high power density electronic device cooling, high power laser thermal management, food processing and other chemical, aerospace and military fields. Increasing the boiling heat transfer performance is of great significance in improving the efficiency, safety and system cost of the energy system, and can effectively achieve energy saving and emission reduction.
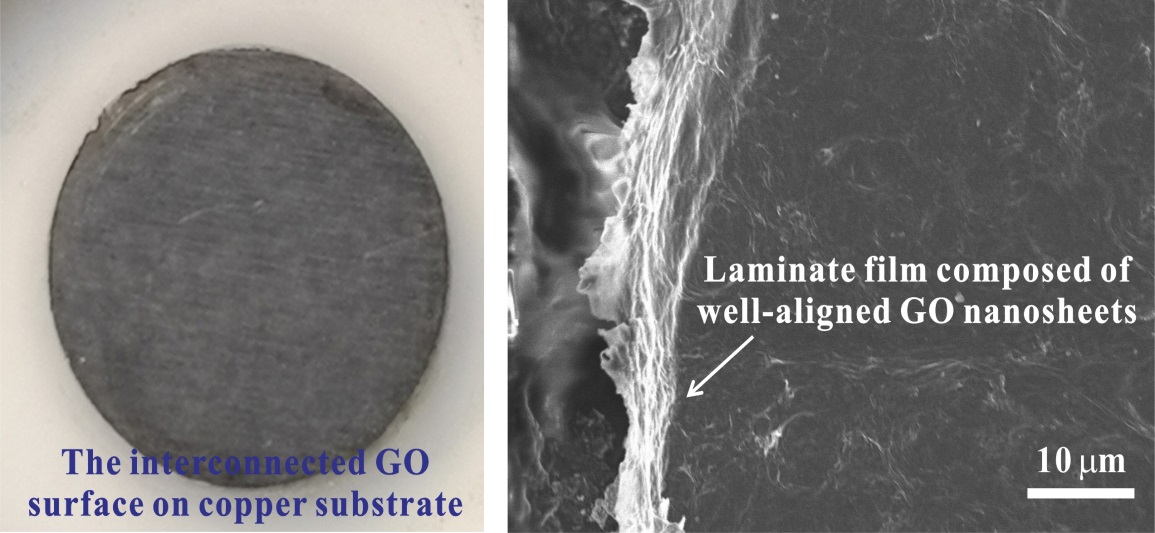
Carbon nanomaterials such as graphene have excellent mechanical, thermal and chemical stability. In recent years, scholars have paid great attention to the enhancement of boiling heat transfer. The boiling enhancement technology based on carbon nanomaterials can be mainly divided into nanofluid technology and nano coating technology. Nanofluid technology uses nanofluids containing carbon nanomaterials instead of water as a liquid working fluid to enhance boiling heat transfer performance. However, the nanoparticles will continue to deposit during the boiling process, and it is difficult to obtain a stable structural surface. Unfavorable factors such as increased thermal resistance caused by excessive nanoparticle deposition and pore filling may cause a decline in boiling performance. Therefore, the use of nano-coating technology to form a stable nanostructure surface on the substrate, so as to achieve the enhancement of boiling heat transfer is very promising. At present, scholars mostly use chemical vapor deposition, layer deposition, and electrochemical methods to construct carbon nanostructured surfaces on heat transfer substrates to significantly improve boiling heat transfer performance. However, these preparation methods are complicated, require high equipment, and have long processing cost and time, and are not scalable, and it is difficult to implement large-scale engineering applications.
To this end, the researchers of the Photoelectric System Thermal Management Team of the Heat and Mass Transfer Research Center of the Institute of Engineering Thermophysics, Chinese Academy of Sciences, under the support of the National Natural Science Foundation of China Youth Science Fund Project (No. 51706225), have studied the low-cost, easy-to-implement The nucleate boiling self-assembly method and the successful preparation of the graphene oxide (GO) boiling surface were excellent. By carefully selecting and regulating the self-assembled deposition parameters, the optimal graphene two-dimensional laminated structure surface was obtained. The heat flux density and heat transfer coefficient are 261 W cm-2 and 9.1 W cm-2 K-1, which is 104% and 73% higher than the original copper plane, reaching the international advanced level and showing excellent durability. Through the visualization of the bubble dynamics behavior of different surfaces, combined with the characterization and analysis of microstructure, wettability, roughness, thermal reduction effect and thermal activity, the mechanism of enhanced boiling heat transfer on GO surface was revealed. Relevant research results were published in the international academic journal Carbon.
The GO self-assembled boiling surface in this study is highly scalable and can be formed on a variety of substrates and expanded to larger areas. In addition, this planar enhanced boiling structure can be extended to a three-dimensional enhanced boiling structure, which will further greatly increase the heat transfer heat density and heat transfer coefficient. The GO self-assembled surface has great advantages in engineering applications, and it is expected to solve the problem of heat dissipation "card neck" of high power density electronic devices in practical applications, and improve the efficiency, cost and safety of the energy system.
QUANTUM
En Masse and Drag Chain Conveyors are used to convey powdery and granulated
products across a range of inclined and vertical installations.
QUANTUM
utilizes drop-forged links with case hardened pins, or standard conveyor chains
depending on the material to be conveyed & the application.
The
conveyor length is limited by the capacity and chain speed, but lengths of 100m
and more are not uncommon, with capacities over 600t/hr.
The
standard range of QUANTUM En Masse Conveyors comes in 2 grades:
• Light: (QCL Range, specifically designed
for typical products Grain , flour, stock feed pellets, paper, pulp->
Specific gravity 750kg/m3)
• Heavy: (QCH Range, specifically
designed for Cement, fly ash, sand, woodchips, biomass, coal powder ->
Specific gravity 1500kg/m3)
All
ranges span from 190-1000mm wide, come with single or dual chain options and have
a variety of standard attachments to suit the application. For Bin discharge, we
provide multiple strand chain & specially designed hoppers for constant
& even emptying.
QUANTUM can provide customized designs, including for high temperature applications and all conveyor arrangement can be designed into horizontal or inclined layout.